When it comes to mattresses there really aren’t that many people that get very excited. So how cool could a mattress factory of all places really be? The answer…so, so, SO cool!
Earlier this week I had the opportunity to tour Brooklyn Bedding’s brand new state-of-the-art factory. Their new factory is located in the heart of Phoenix, Arizona. It is a whooping 145,000 square feet and cost $7,000,000 to construct. It is a BIG place.
Brooklyn Bedding manufactures some of the most popular and well-made mattresses across the US. They are most known for the design and manufacturing of their own brands, Brooklyn Bedding and DreamFoam. Their mattresses are primarily constructed from different types of latex foam, memory foam, polyfoam, and other types of foam.
Brooklyn Bedding and DreamFoam are among a very small number of online companies that actually own their mattress factory. This gives them a great degree of flexibility in terms of design, construction, materials, assembly, and of course offering the best price possible. There’s a lot that goes in to building a new mattress. Covers and other fabric pieces must be woven, cut, and sown together. Foams must be measured, cut, formed, and glued. And of course, all of the individual components must be assembled together into a final mattress before packing the entire thing into a box, ready to be shipped.
REVIEW: Check out our full review of the Brooklyn Bedding mattress
The tour through Brooklyn Bedding was an eye opener for me to be sure. Check out my complete video tour below or scroll below to take the visual tour and discover exactly how your new mattress is created and arrives at your doorstep.
Step 1, The Cover – The process begins with raw textiles. These are woven into what will become the top piece of fabric for the mattress cover.
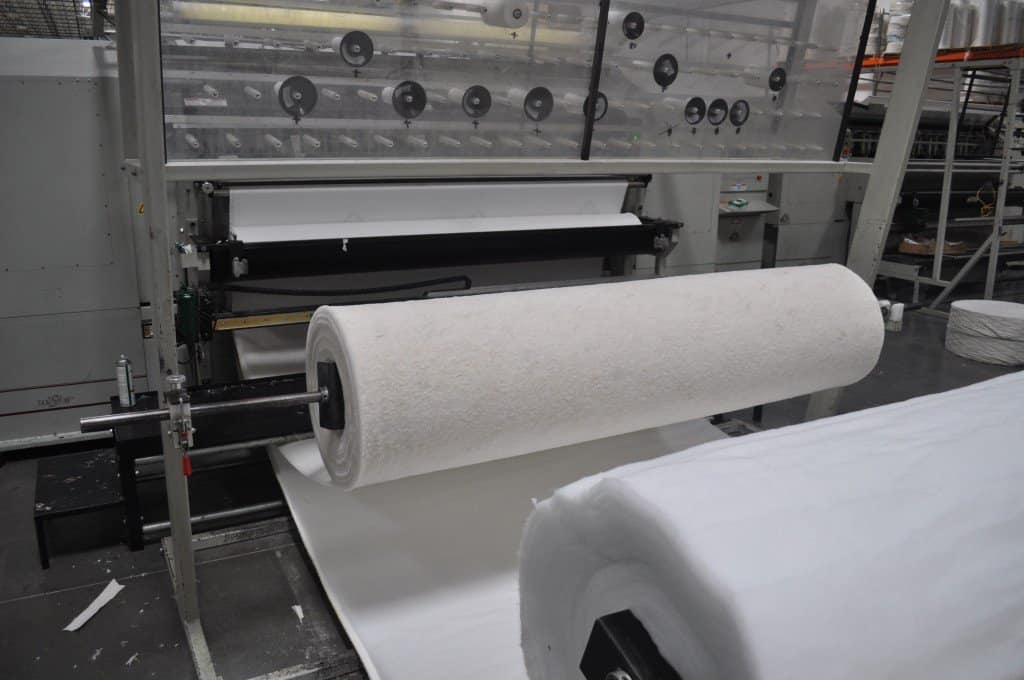
Step 2, Cover Side Panels – A separate, but similar machine, weaves together the the side panel pieces. They are woven in a single sheet and cut, effectively creating about a dozen side panels at a time from a single roll (note the long cuts spread about 6 inches apart).
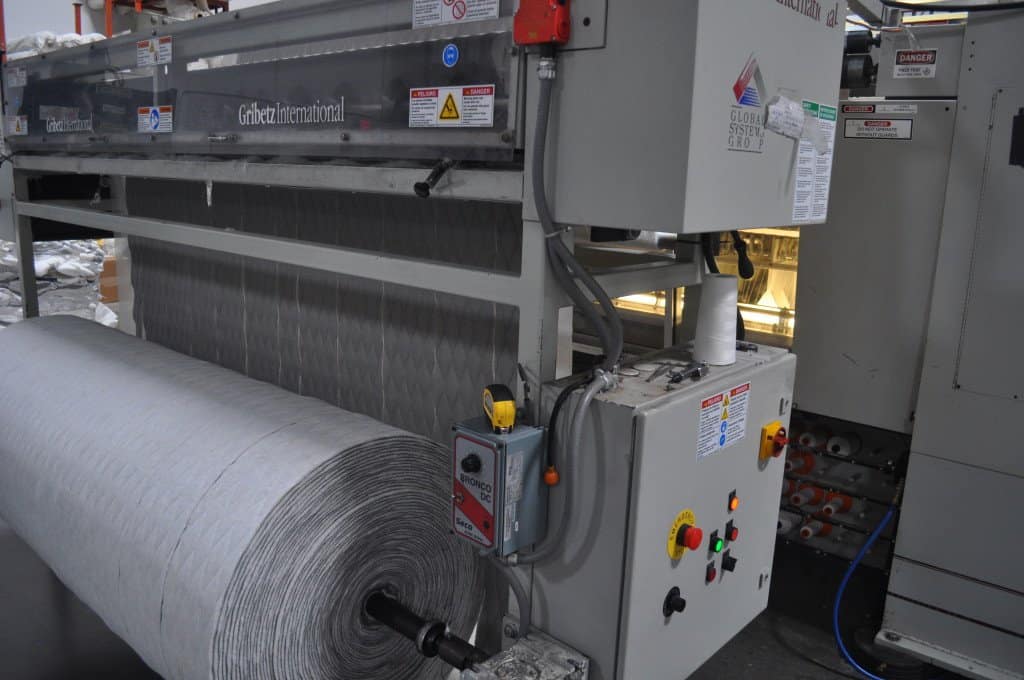
Step 3, Master Seamstresses – Once the cover pieces have been woven together by machines master seamstresses sew the pieces together by hand. It is insane how fast these ladies can move through a cover!
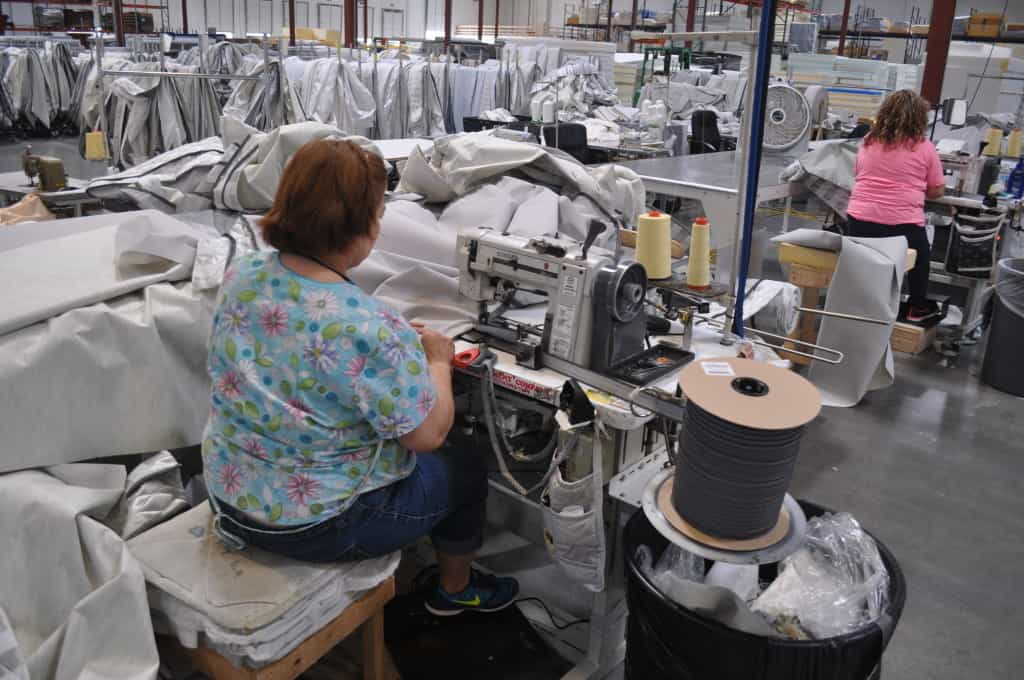
Step 4, Complete Top Cover – This is what a mattress top cover looks like. The thinner pieces of material hanging off the side of the cover will be used to sew the side panels together with the other assembly of the mattress.
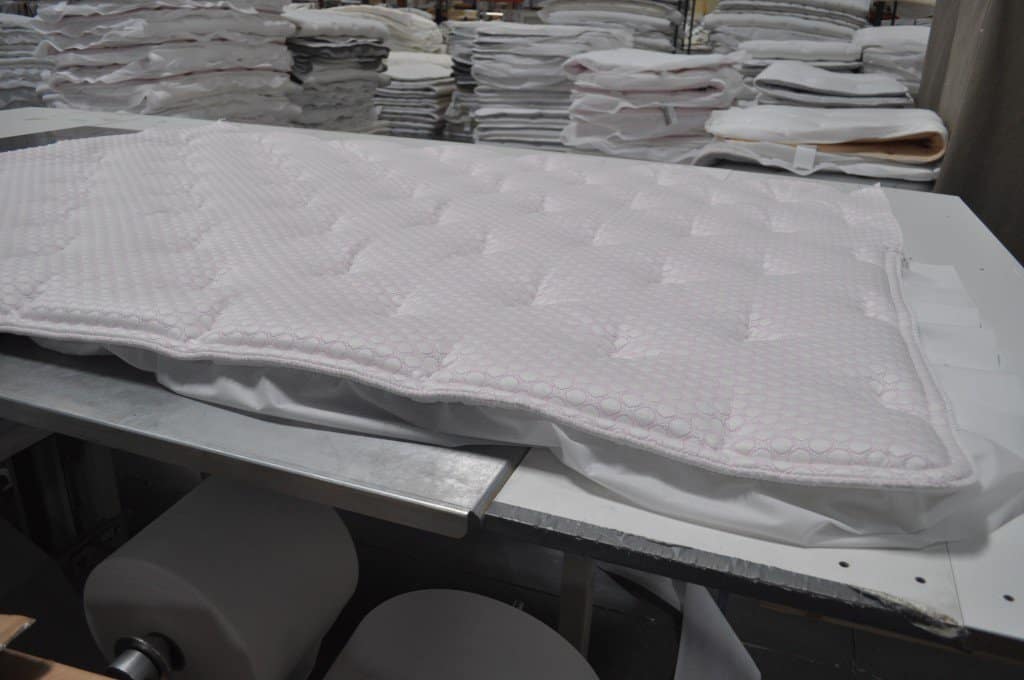
Step 5, Support Foam – At the other end of the factory you’ll find the foam slicing machine. Massive blocks of foam, about 5 feet high, are sent through this machine. It measure the foam and slices the appropriate size off. The foam then travels down the line to the next step. (watch video above to see this machine in action!)
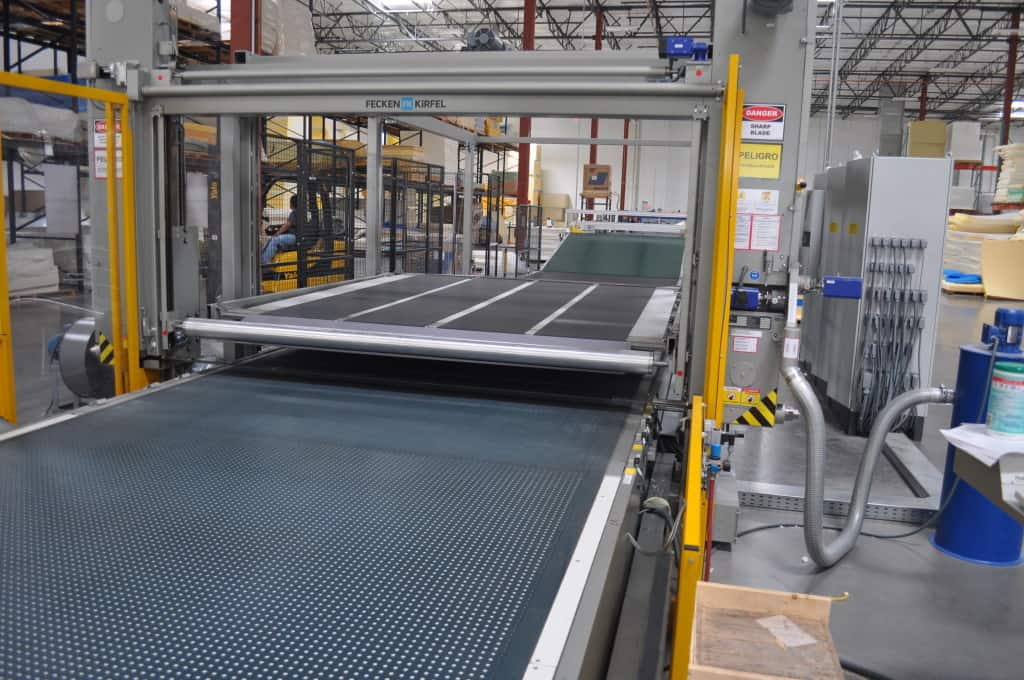
Step 6, Convoluted Foam Core – Next up on the foam line is the convoluted foam machine. It has rows of spinning teeth that cut the foam into 2 equal sections and carve in the convoluted channels. These foam channels allow for better deep compression support and breathability in the foam, improving cooling.
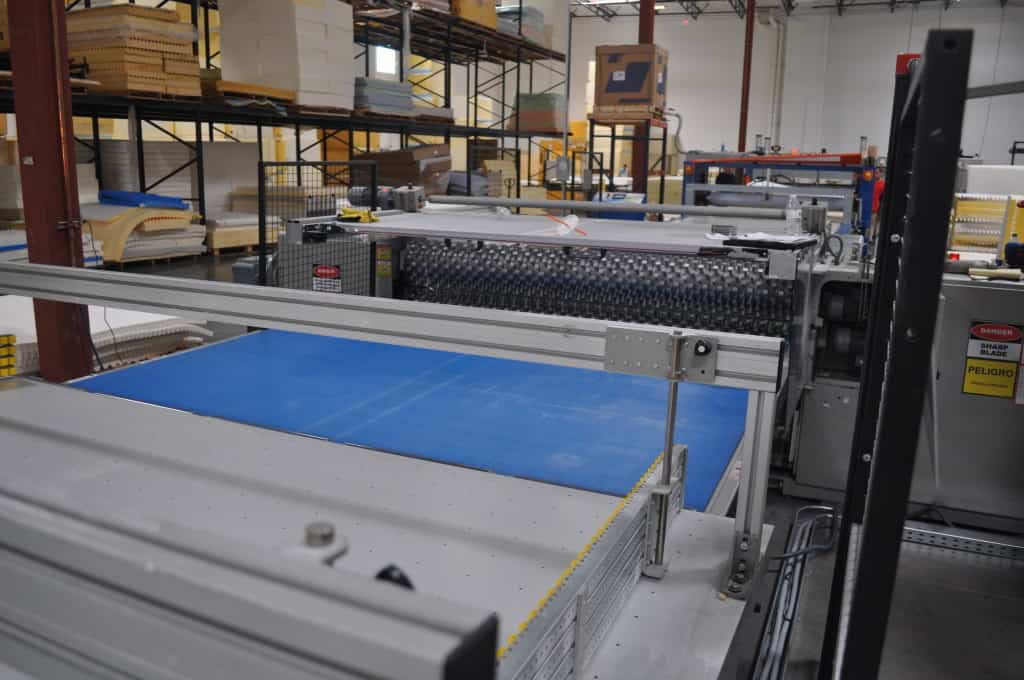
Step 7, Final Foam Cores – This is the end of the line with the completed convoluted support foam. Not pictured is the machine that applies a thin layer of glue. Additionally, after the glue is applied this particular mattress (it’s one of the DreamFoam mattresses) needs two foam layers stacked on top of each other. The machine at the very end here presses these layers together, ensuring they stay bonded permanently.
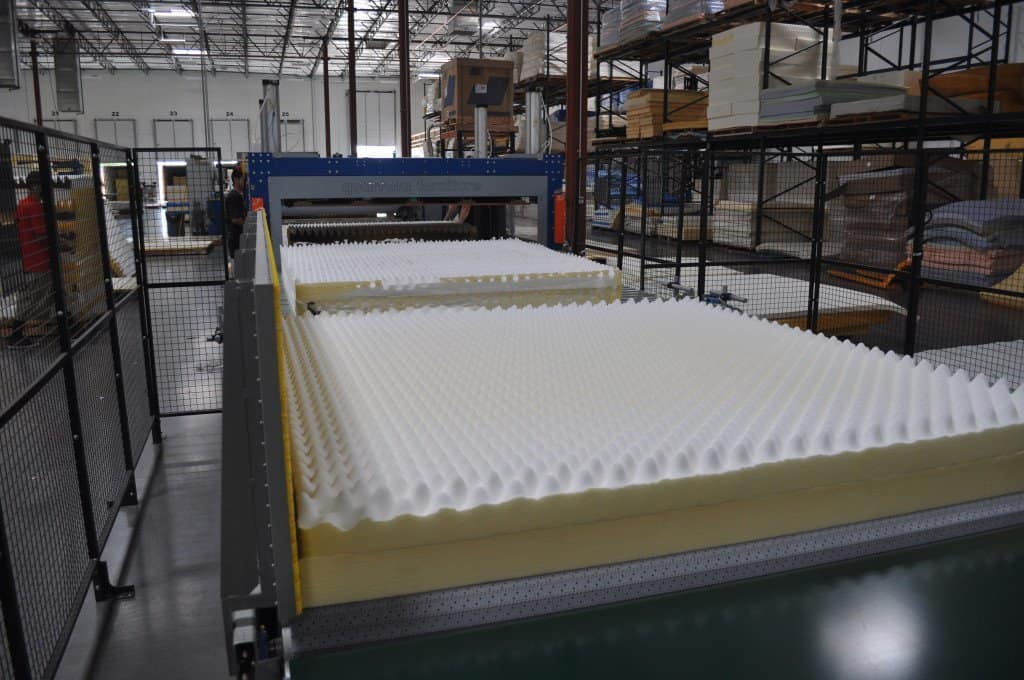
Step 8, Foam Slicer – Once the foam cores are completed they are sent to the cutting station. This machine cuts any excess from the foam, ensuring it is sized appropriately for the mattress it’s going into. Even with an insanely sharp blade and something as easy to cut as foam, the blades must be replaced every 4 weeks due to the sheer volume of cutting. The excess foam is bailed and sold to other companies.
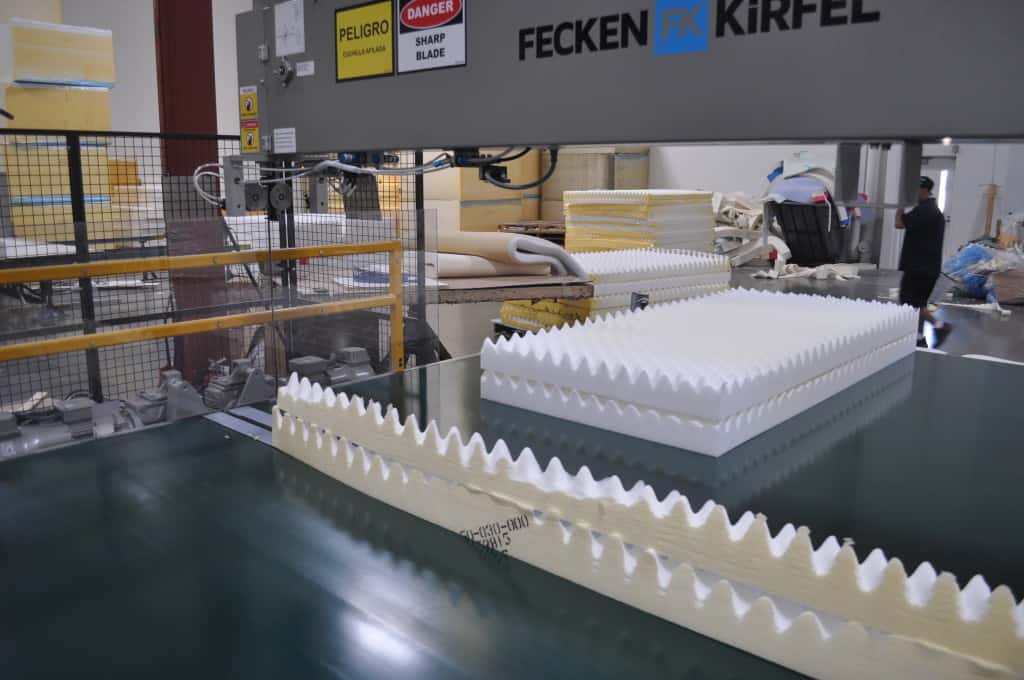
Step 8, Component Assembly – The completed foam cores and covers are brought to the primary assembly line (it sits in the middle of the factory). Workers sew and assemble the components together to form the completed mattress.
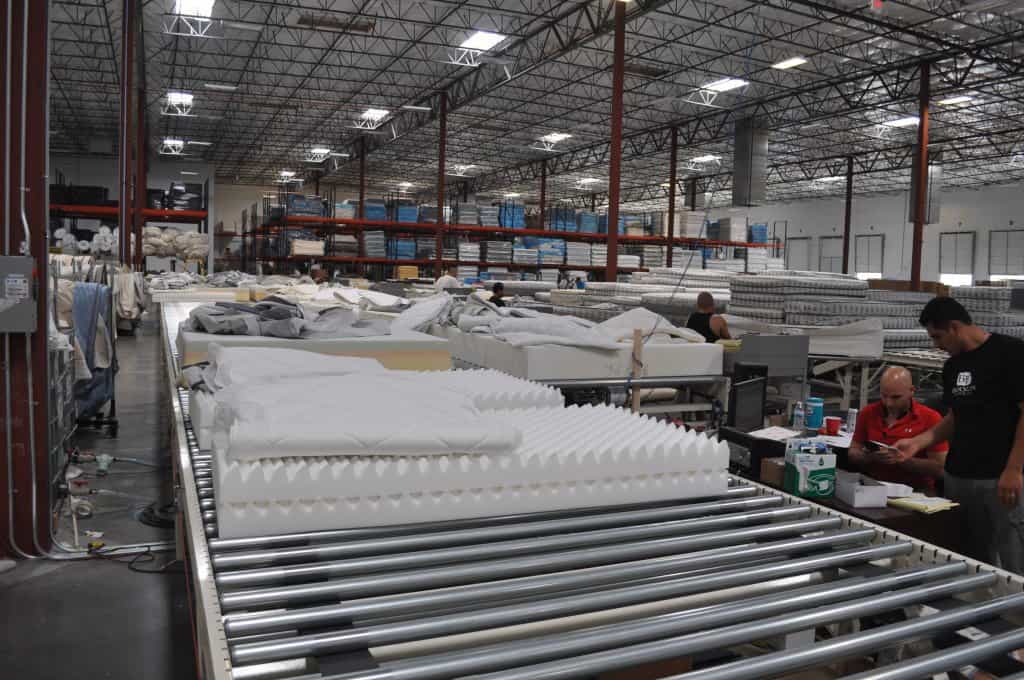
Step 9, Sewing Everything Together – One of the most skilled positions on the factory floor are the workers who sew the completed cover and side panels together within the foam structure. There is very little room for error. Massive industrial sewing machines rotate around the perimeter of the mattress (they sit on a rail type of a system). Havier (pictured in the white shirt in the middle), is an artisan when it comes to this work. He’s been working with Brooklyn Bedding since they created their first mattress in 2001.
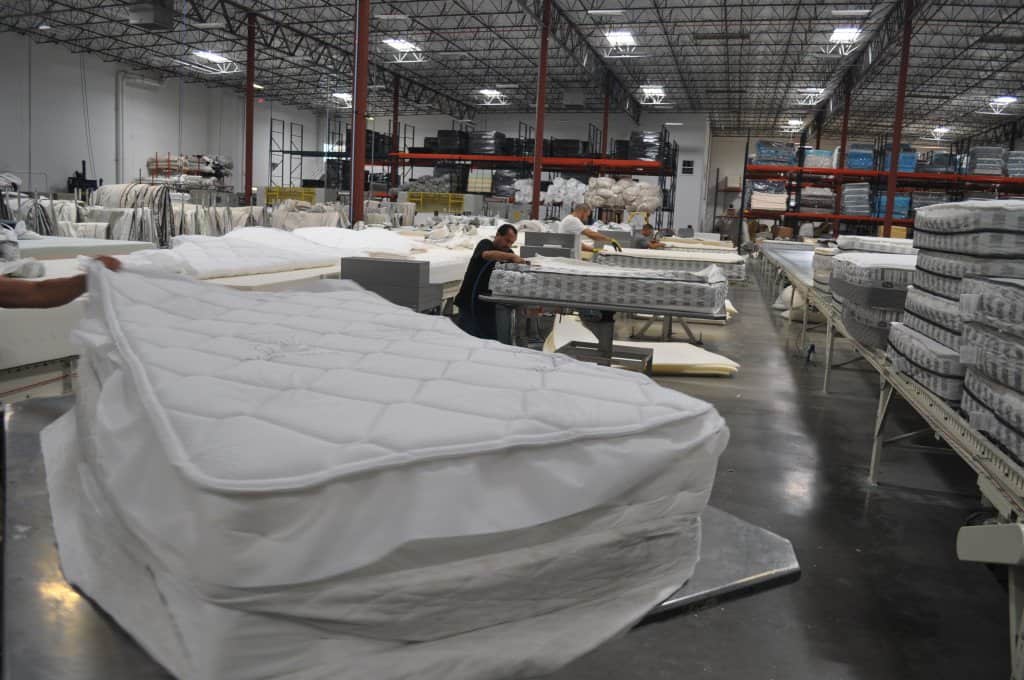
Step 10, Compressed for Shipping – Once the mattresses are completely assembled they are sent to the 1 of 4 roll packing machines. The simpler machines cost $125,000. This advanced roll packer is $400,000 and compresses the mattress both on the sides and top before final vacuum sealing it. This allows a King mattress to fix into a 19 x 19 x 45 inch box.
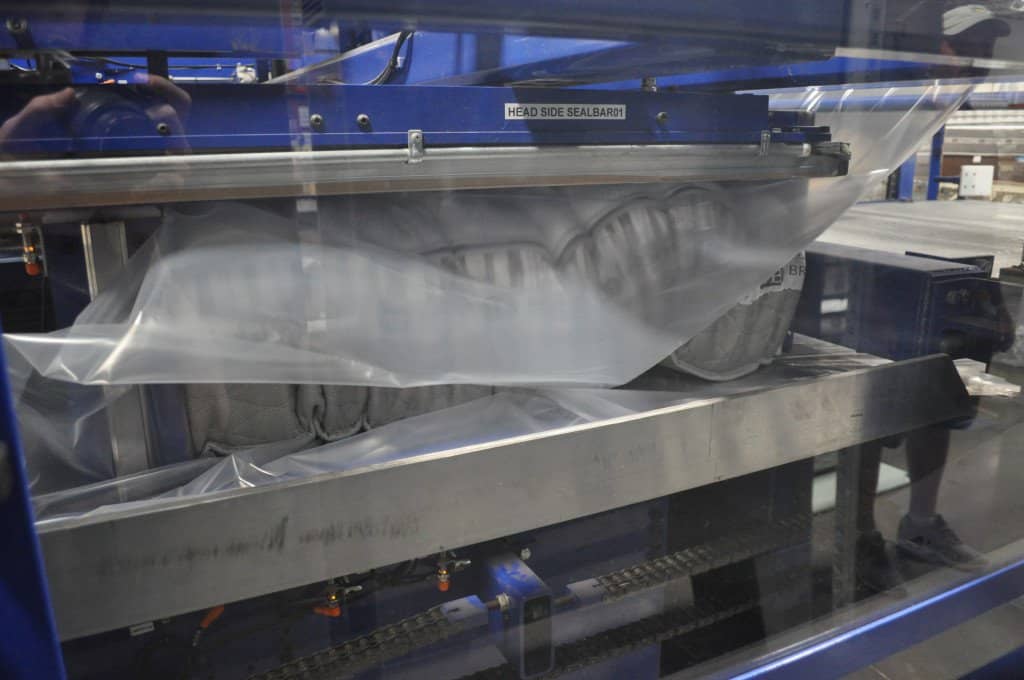
Step 11, Enjoy – That’s it! Mattresses are shipped all across the country. Below is their newest mattress, the Brooklyn Bedding mattress uncompressed and on my King sized platform bed.
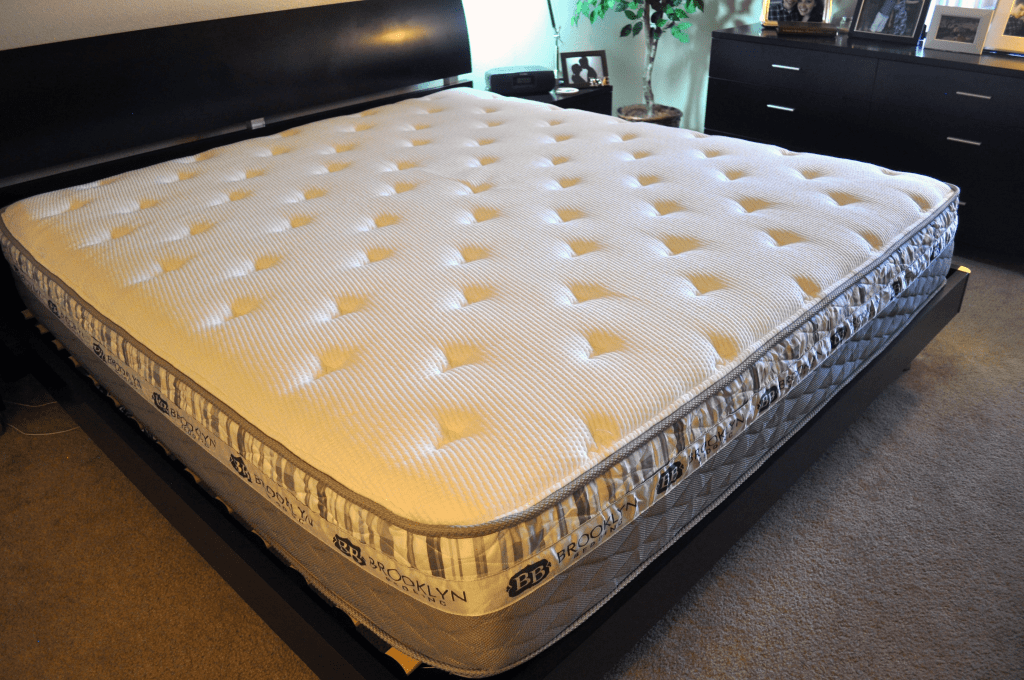